|
PROJECT DESCRIPTION
Introduction
This section describes the project proposed by the project proponent, SCE. The section describes the valuation required by AB 1890, the sale that SCE has proposed to value its share of the MGS, a summary of the existing facilities at the MGS, and the physical improvements directly associated with the sale. An aerial photograph of the facility is presented in Figure 2-1.
Sales and Valuations
SCE is required by AB 1890 to determine the value of its 56% share in the MGS, by December 31, 2001 (AB 1890 requires many utility-owned generation assets to be valued using appraisal, sale, or other divestiture). SCE has proposed to determine the value of its share of the MGS by sale using an auction process. The valuation proposal is contained in SCEs Section 851 Application submitted to the CPUC. The proposed project is the SCE auction process and the sale of SCEs interest in the MGS.
SCE has proposed that a fence be constructed to separate the switching yard from the generating facilities at the MGS because SCE does not propose to sell the transmission facilities that include the switching yard. The sale of the MGS would result in a direct physical change to the environment if the 500-foot long fence is constructed. See Figure 2-2, which illustrates the location of the proposed fence. Construction of the fence will require a building permit from Clark County. Potential impacts of fence construction are evaluated in Chapter 4 (Initial Study).
Connected Actions
Project descriptions under CEQA are required to account for reasonably foreseeable future phases, or other reasonably foreseeable consequences of proposed projects. A two pronged test to identify reasonably foreseeable projects requires that an EIR must include an analysis of an action if: "(1) it is a reasonably foreseeable consequence of the initial project; and (2) the future expansion or action will likely change the scope or nature of the initial project or its environmental effects." (Laurel Heights Improvement Association of San Francisco, Inc. v. Regents of the University of California, 1988).
FIGURE 2-1: Mohave Generating Station Aerial View
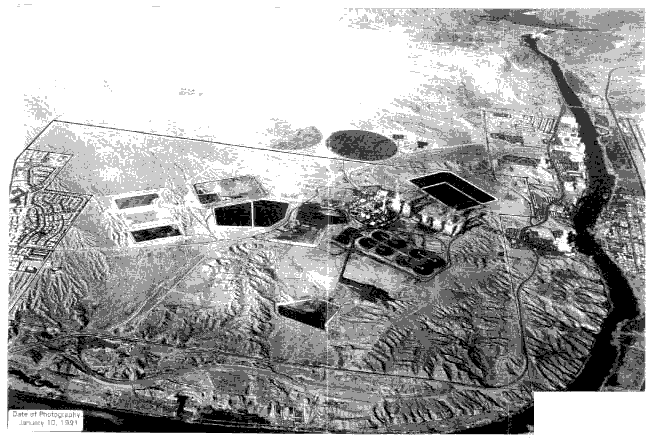
Figure2-2: Mohave Annotated Site Map
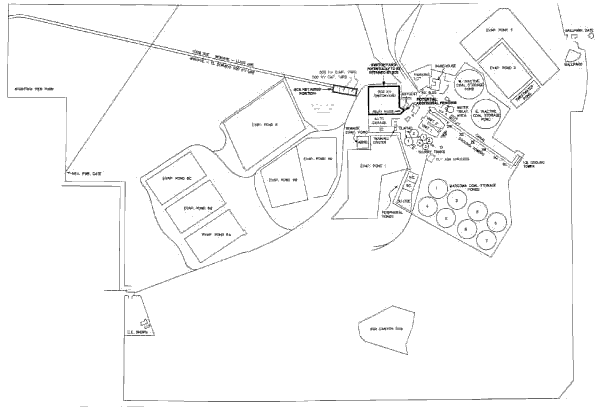
POSSIBLE CONNECTED ACTIONS
There is a range of possible actions that could occur if SCE sells its share of the MGS. These actions may be induced by the sale; some of the induced effects could result in physical changes to the environment.
Possible connected actions described below include:
Continued existing operations
Increased plant output
Section 3, the next section in this document, contains additional information about reasonably foreseeable connected actions that could be associated with the sale, and that are therefore analyzed in this Initial Study.
Continue Existing Operations
In this scenario, the operations at the MGS would be essentially the same as are currently occurring. The MGS could continue to curtail generation (in the range of 1 to 3% of capacity) for economic reasons. Under this scenario, the MGS could continue to operate within the confines of existing permit requirements.
Increase Plant Output
The MGS output could be increased because the plant is not currently running at maximum output. New owners of the MGS could increase output by changing maintenance practices. Changing or modifying equipment that is currently at the MGS could also increase output. A new owner could increase generation by up to 10% (provided this occurs within air permit constraints) without any discretionary approval, if the new owner could find a market for this additional energy output.
Mohave Generating Station Existing Condition
The existing condition at the MGS is provided below to facilitate the evaluation of project impacts. The description is based on the MGS PEA (Entrix 1999), and on additional information provided by SCE in response to CPUC data requests.
The MGS is a 1,580 MW coal-fired power plant located in Laughlin, Nevada. The plant is jointly owned by SCE (56%), LADWP (20%), NPC (14%), SRP (10%). SCE is the operating agent, operating the plant on behalf of the participants.
SITE LOCATION
The MGS is located at the southern tip of Clark County, Nevada. The station covers approximately 2,490 acres and is approximately one mile west and north of the Colorado River in Laughlin. The station is located in Township 32, South Range 66 East MBD&M in Sections 22 and 23 and part of Sections 21, 24, 26 and 27. The plant site is accessible from Nevada State Route 163, Edison Way, and Desert Road.
The generating units are built on a plateau with arroyos dipping downwards to the river on the east and south. An upward-sloped plain rises northwest to the mountains. Units 1 and 2 are at datum elevations of 712.00 above mean sea level (MSL) and are situated on the northeastern portion of the property. The remaining portions of the site contain the ash disposal area, evaporation ponds, coal storage ponds, and undeveloped property.
MGS DESCRIPTION
The MGS has two coal-fired units, each rated at 790 MW. Commercial operation of Unit 1 and Unit 2 began in 1971. The facility was originally designed and built as a base-load plant. In other words, the plant was running all the time unless its operations were curtailed for maintenance and other reasons, such as opacity (plume opacity is the measurement of how dark a plume appears against the sky at the point it exits the stack). With changing market requirements, the units load is sometimes reduced during off-peak hours. The normal range of load for each unit varies between 350 MW and 750 MW. The average annual capacity factor of the Plant from 1990 to 1998 was 71.5%. The capacity factor is a measure of the actual generation of a unit, compared to the design generation (790 MW per unit).
The main steam generators are pulverized coal-fueled, tangentially fired, once through, combined circulation, super-critical, multi-stage superheat, multi-stage single reheat design. Coal is supplied to the station via pipeline in a slurry consisting of approximately 50% coal and 50% water.
Coal Slurry Handling and Processing System
Coal is mined by Peabody Coal Company at Black Mesa Mine in northeastern Arizona. The coal is crushed, mixed with water, and transported 273 miles through an 18-inch diameter pipeline to the station (the diameter changes to 12 inches for the last 12 miles). Neither SCE nor the station have any ownership interest in the mine or the pipeline. The station takes ownership of the fuel once it reaches the station, where the coal slurry is pumped into one of four storage tanks, each with a capacity of approximately 8 million gallons, or to one of eight Marcona storage ponds. From the storage tanks, the coal is passed through a series of high-speed centrifuges that spin out 75% or more of the water. From the centrifuges, the coal slurry is fed into the coal pulverizers for drying and grinding. A total of 20 pulverizers (10 per unit) receive the coal slurry from the centrifuges. Each pulverizer is a self-contained unit which can produce 90,400 pounds of pulverized coal per hour, pulverizing to a fineness of 70% through a 200 mesh screen at a maximum moisture content of 25%. Air supplied by the primary air fans transports the dry coal through the coal fuel pipes to the boilers for combustion.
The centrifuged water contains a small amount of coal fines. This water is processed in one of two clariflocculators (one per unit) which are approximately 200 feet in diameter and 20 feet in height. Flocculants are added to allow the coal to settle to the bottom where it is recaptured and then sent back to boilers to be burned. Much of the remaining water is added to the condenser cooling water as make-up. Seven cooling towers circulate a total of 540,000 gallons of water per minute to cool the two generating units.
Two facilities at the MGS are used solely for coal storage: (1) the four "active" slurry storage tanks that supply fuel directly to the boilers; and (2) the eight Marcona ponds. During normal operation, the coal slurry pipeline is directed to one of the four active slurry storage tanks. Should these become full, the slurry is diverted to one of the eight Marcona ponds for storage. During full load operation of the Plant, coal slurry from the Marcona ponds is used to supplement the coal slurry provided by the slurry pipeline.
The Marcona ponds are conical storage ponds, 436 feet in diameter and 40 feet deep, with 4-inch thick asphaltic concrete inside surfaces and bottom surfaces. Each pond has a capacity of 3,040,000 cubic feet or 80,000 tons of coal. When full, the eight Marcona ponds can provide a 40-day supply of fuel to both generating units at the MGS. The Marcona ponds are designed to operate with at least 2 inches of water on top of the coal when coal is not being reclaimed from the ponds. This water cap prevents the coal from drying out and eliminates the potential for spontaneous combustion. This water also facilitates the coal removal process by keeping the coal water-saturated, thus improving the flow characteristics.
The coal dump pond may be used to receive coal slurry when both the active coal slurry tanks and the Marcona ponds are full. The coal dump pond acts as a settling basin for the coal, which can be removed by reslurrying and pumping it back to the Marcona ponds when space is available. By design, the coal in the coal dump pond is always kept under a water cap and is pumped out as a slurry.
Ash System
The ash produced in the combustion process consists of bottom ash, fly ash, and economizer ash. Each is described in the following paragraphs.
Bottom ash is a coal ash collected at the bottom of the steam generating units, and is directed to the bottom ash hopper. From there, the bottom ash is crushed and mixed with water, and pumped as a slurry to one of the dewatering bins. Each dewatering bin is 35 feet in diameter with a storage capacity of 24,000 cubic feet, or 444 tons with a bottom ash density of 37 pounds per cubic foot. The ash is dewatered and stored in the bins, with the water drained from the ash collected in settling and surge tanks. Each bin is elevated for truck clearance with trucks periodically hauling the ash from the dewatering bins to the ash disposal area onsite.
Fly ash, which is removed by the electrostatic precipitators (ESPs) used for air emission control, constitutes approximately 70% of the MGSs total ash output, and is produced by each unit at a rate of around 40 tons per hour during full load conditions. For each ESP, the fly ash is collected in 32 hoppers. From the hoppers the fly ash is conveyed to the fly ash silo. The silo has a storage capacity of 2,020 tons of fly ash and provides nearly 26 hours storage for both boilers operating at full load. The contents of the storage silo are regularly emptied into trucks and disposed.
A truck loading station is located below the storage bin and consists of four rotary unloaders. The dry ash is mixed with water prior to being unloaded into 135 cubic yard capacity bottom-dump trucks, which remove the material.
Economizer ash accumulates below the economizer in the economizer ash hoppers. There are six hoppers per unit, each designed to handle a maximum of 5 tons per hour. Each hopper empties into a water line where it is slurried and gravity fed into the bottom ash hoppers.
Ash Disposal
Ash from the MGS is disposed of in an on-site canyon that is approximately 360 acres in area, and is located approximately 0.7-miles south of the power block. The canyon is referred to as Ash Canyon.
Ash Canyon is situated in a natural wash contained by an earthen dike, known as Ash Canyon Dam. The function of the dam is to collect any surface runoff from the disposal area and thus prevent it from leaving the Plant property. Through 1993, approximately 8,500,000 cubic yards of material had been disposed of in Ash Canyon. The landfill is expected to be at capacity in the year 2025 (HSI-Geotrans 1998). Ash Canyon has been designed to contain all wastes produced during the lifetime of the plant. Since 1978, the MGS has sold fly ash to Boral Material Technologies for use as a concrete additive. Presently, 99% of fly ash generated is being sold.
Ash Canyon is permitted as a Class III disposal area and is not permitted for the disposal of hazardous material. Material disposed of at Ash Canyon consists of bottom ash, fly ash, construction debris, and the evaporation pond sediments. The disposal process involves putting down layer upon layer of fly ash, bottom ash, sludge, and coal waste from the coal dump pond, then covering the layers with earth. The various layers are compacted daily. Approximately 160,000 cubic yards of bottom ash and 60,000 cubic yards of sludge are landfilled annually.
A series of groundwater monitor wells are installed within the Ash Canyon disposal area and south of Ash Canyon Dam. These wells were installed to ensure that leachate from the disposal area is not impacting groundwater beneath the site.
Plant Water System
The MGS is a zero discharge facility in terms of wastewater emanating from the Plants processes. Wastewater is managed through the use of evapo-ration ponds, a vapor recompression brine concentrator, and control of the stations water balance. The primary makeup water source for the Plant is pumped from the Colorado River. The Plant has an average requirement of 15,000 acre feet of water per year for plant cooling, process water, and domestic water purposes. Water separated from the coal slurry is utilized as makeup water to the circulating water system. The river water is first treated in a lime/soda water softener to reduce the overall dissolved solids prior to being used as makeup water for the closed loop circulating water system.
The water intake facility is located due east of the plant and north of Harrahs Casino on the Colorado River in a river pump house. The pump house contains three pumps that supply river water to the station. Each pump is suitable for parallel, standby, and continuous operation at any discharge rate from a continuous minimum flow of 250 gallons per minute (GPM) to a maximum flow of 8,400 GPM. During normal operation, two pumps are in service with the third in standby. Summer temperatures can cause the make-up rates to average 17,000 GMP; winter rates may average as low as 5,000 GMP.
Excess water is removed from the station through evaporation only. Evaporation occurs first in the cooling towers and then in the stations lined evaporation ponds. Water that is unusable due to high salt content or solids is sent to one of the six wastewater evaporation ponds. The largest contributor to the wastewater ponds is from the open circulating water system. Water from the open circulating water system is pumped to the brine concentrator, which concentrates the salts by a factor of 10 and then sends the concentrated solution to the wastewater ponds. Two other wastewater streams are the lime/soda ash softener sludge and the effluent of the station sewage treatment system.
There are a total of 13 evaporation ponds at the MGS. The four primary wastewater ponds are Ponds 3, 6A, 6B, and 6C. Pond 3, located northeast of the Plant, has a surface area of 36.4 acres and a yearly evaporation capacity of 65 million gallons. Ponds 6A, 6B, and 6C are located west of the Plant and have a surface area of 20 acres each and a yearly evaporation capacity of 35.74 million gallons.
When the solid deposits in the wastewater ponds become fairly deep, their chemical composition is analyzed to determine if they contain hazardous compounds. Once verified to be non-hazardous, the deposits are loaded into a bottom-dump truck and disposed of in the on-site landfill. The operation occurs approximately every seven years.
Should an unforeseen situation result in all of the four primary wastewater ponds being unavailable, Ponds 2 and 4 can be used as back-up. Pond 2, normally the primary reclaim pond, has a surface area of 18.8 acres and a yearly evaporation capacity of 33.6 million gallons. Pond 4, the largest evaporation pond, is divided into 4A and 4B. 4A is normally used to contain the treated effluent from the Plants effluent (treated sewage) system. 4B contains wastewater. With a surface area of 55 acres, Pond 4 has an evaporation capacity of 98.3 million gallons per year.
Ponds 1 and 5 originally collected coal recovered from the clariflocculators (which is now burned in the boilers). The coal was allowed to settle in the ponds, the water decanted or evaporated, and the material covered with overburden. The ponds now contain coal with a moisture content ranging from 40% at the bottom of the pond to approximately 10% near the top. In 1985, the coal deposits in Ponds 1 and 5 were sold to Fly Ash Haulers, Inc. to mine and process the coal into pellets on-site. The pellets were then hauled off-site to be burned at the Biogen Power Plant (Biogen) located northwest of Laughlin in California. Biogen ceased its operations in the early 1990s. In 1997, Mohave Fuels, a consortium of Fly Ash Haulers and Salvage Industries, agreed to purchase the remaining 300,000 tons. They currently pelletize the underflow before trucking it offsite.
The north and south peripheral ponds are located next to the Marcona ponds and are used to store surface run-off and drainage from the ditches and canals on-site. The solids settle to the bottom of the pond, and are then pumped into the adjacent southwest peripheral sludge drying pond. The material is dried by turning it over every other day. On approximately a three month cycle, the sludge is removed by a front-end loader, placed into an end dump truck, and hauled to the on-site landfill.
All of the evaporation ponds are lined with an impermeable membrane liner. With the exception of Pond 5 and the peripheral ponds, each pond has a network of resistivity cables underneath it, which are used for leak detection. There are 76 monitoring wells located around and downgradient of the ponds.
Natural Gas Supply
Natural gas supplied by Southwest Gas Company (SGC) is utilized for ignition purposes and for the primary air burners used in start-up conditions to heat the transport air for the pulverizer mills. The gas is supplied to the station through a 20-inch gas pipeline that enters the plant from the south. MGS was designed to burn coal, so full operation on gas would require extensive retrofits to the station and pipeline expansion. Also, gas use in excess of 15% of the stations full-load capability is not allowed by the plants Colorado River water rights, which are conditioned on the use of coal from Black Mesa.
Transmission System
The MGS is interconnected to the California Independent System Operator (ISO) controlled grid via the Mohave-Eldorado and Mohave-Lugo 500 kV transmission lines. The conductors of these lines are capable of up to 3950 amps, approximately 3590 Mega-volt-amps (MVA) (i.e., million volts-amps). The Mohave-Eldorado line has a wavetrap and disconnect switch equipment limitation of 3000 amps, approximately 2725 MVA. The Mohave-Lugo line has a series capacitor equipment limitation of 1600 amps, approximately 1453 MVA. The transmission lines are not part of the asset valuation, and would not be sold with the station.
Air Emissions
Each generating unit is equipped with electrostatic precipitators which remove fly ash from the flue gases generated by the combustion process. Precipitators operate at 99% efficiency. Gases leaving the precipitator enter a 500-foot chimney common to both units. Continuous Emissions Monitoring systems (CEMs) are installed in the ducts of both units to monitor nitrogen oxide and sulfur oxide discharges. In addition, a Continuous Opacity Monitor (COM) is installed in the stack. Nevertheless, in 1997 the plant contributed:
2,607 tons per year of PM10
41,354 tons per year of SO2
1,369 tons per year of CO
20,563 tons per year of NOX
159 tons per year of reactive organic gas (ROG)
0.95 tons per year of lead
MGS PERFORMANCE
From its commercial operation in 1971, until the early 1990s, the MGS was operated as a base-load plant. Since that time, the plant has still fundamentally operated as a base-load plant, but reduced demand has led to some reduced production during night hours, when system load requirements are at a minimum. This section quantifies the MGSs annual energy production since 1990, and describes the limitations to full-capacity operation.
Annual Production
The MGSs production performance since 1991 is summarized in Table 2-1. The capacity factor dropped from 76% to 71% in 1993, reflecting the implementation of a more stringent opacity standard (for air quality). The MGSs net transmitted energy since 1991 has been above 9,600 gigawatt-hour (gwhr), and for three years was in excess of 10,000 gwhr. The station set a record high generation level in 1992 of 10,620 gwhr.
Table 2-1: Yearly Performance (1990-1998) (in percent)
|
1990 |
1991 |
1992 |
1993 |
1994 |
1995 |
1996 |
1997 |
1998 |
Capacity Factor |
64.3 |
76.18 |
76.52 |
71.20 |
71.83 |
73.38 |
70.61 |
70.08 |
69.67 |
Availibility Factor |
70.69 |
82.29 |
86.99 |
86.22 |
86.18 |
87.42 |
84.96 |
84.34 |
85.62 |
Full Forced Outage Rate |
13.07 |
9.67 |
8.67 |
7.84 |
2.78 |
5.86 |
9.16 |
9.35 |
6.59 |
Partial Forced Outage Rate |
6.39 |
6.12 |
10.47 |
15.02 |
14.35 |
14.04 |
14.35 |
14.26 |
15.95 |
Use Factor |
90.95 |
92.57 |
87.96 |
82.58 |
83.35 |
83.04 |
83.11 |
83.10 |
81.37 |
a) Capacity Factor The ratio of energy produced during a given time period, measured in kilowatt hours, to the energy the unit could have produced if it had been operating at its rated capacity during that time period, expressed in kilowatts.
b)Availability Factor The ratio of a utility systems available hours to the rated capacity of the system.
c) Full Forced Outage Rate The ratio of the number of hours a facility was out of service during a certain time period to the total number of hours in that period.
d) Partial Forced Outage Rate The ratio of the number of hours a facility was lower than the rated electrical capability to the total rated electrical capability.
e) Use Factor The ratio of a utility systems peak load to the rated capacity of the system.
*SOURCE SCE 1999 and PG&E 1992
Physical and Regulatory Constraints on the MGS Operations
The annual capacity factor discussed in the previous section compares the actual amount of time and output of the plant to the theoretical maximum time and output (that is, the rated capacity). The annual capacity factor at the MGS is limited by both permit constraints and by equipment limits. As an essentially base-loaded plant, the MGS is currently operated to nearly the full amount allowed by these limits.
Five operating conditions limit the full-capacity operation of the MGS:
Permit limits on the opacity of the air discharge plume
Process input limits such as feedwater flow and fuel supply
Equipment maintenance
Market-based demand
Condensate temperature
Each limitation is described in more detail in the following text.
Opacity of the air discharge plume is the most frequent limitation to plant operation. The MGS is currently limited to a 30% opacity using a 6-minute average. This limit was adopted in 1992 by the Nevada State Environmental Commis-sion which reduced the plants existing opacity limit to a 40%, 6-minute limit in 1993, and a 30%, 6-minute limit in 1994. In two of the last three years, the opacity limit has been the most frequent cause of lost load; in the other year it ranked third. When both units are on line, the load is often limited to between 600 and 700 MW each, compared to the rated capacity of 790 MW each. The amount of opacity is a function of several factors such as coal quality, equipment and control system performance, local meteorology, and others. Opacity is not specifically tied to a certain load point, but can vary based upon the interplay of these factors.
Process input limits are due to those inputs to the station that, when limited, can reduce the ability of the Plant to produce at full output. Both fuel and water are process input limits. Feedwater flow, that is, the rate at which water can be delivered from the Colorado River intake and other sources, limits station capacity. The feedwater flow rate limitation is encountered primarily in the winter months, or upon return to service from an outage. During the summer months, the circulating water temperature can also limit production, since the warmer circulating water through the condenser tubes increases condensate temperature and the turbines back pressure. This limits the load to 765 MW, compared to the rated capacity of 790 MW. Currently, the MGS has enough water allocated to it to operate within historic capacity factors. Interruptions in the fuel supply could also limit station operation. Additional fuel is stored on site for this contingency.
Maintenance also affects the stations capacity and annual capacity factor. When certain major equipment is removed from service for scheduled repair, the impacted unit must be shut down completely, thus reducing the output from that unit. Similarly, unscheduled maintenance also requires the shutting down of power-producing units, with a corresponding reduction in the annual capacity factor. The most frequent cause of forced outages is control equipment trips, which are designed to detect run conditions outside specifications.
Because SCE bids its MGS output into the California Power Exchange, it will only bid its output when the market price for energy exceeds the incremental cost of operation for its ownership share. Such market limits to production have been insignificant since deregulation.
Condensate temperature is set at 135°F to protect the low-pressure turbine. This limit is rarely encountered.
Ancillary Facilities Not Part of the Sale
There are several ancillary facilities not part of the valuation, the most important are discussed below. Except for the switchyard, the retention by SCE of its interest in these ancillary facilities and sale would not require construction, fencing, or any other physical change in conjunction with a change in plant ownership.
Transmission System. As part of the transmission system, there are both a jointly owned 500-kV switchyard and a Nevada Power Company (NPC)-owned switchyard at the MGS. The owners may retain ownership of the 500-kV switchyard. In this case, approximately 500 feet of fencing may be installed to extend existing fencing and isolate the switchyard. The fencing will be on currently-paved property. There is also a 500-kV capacitor yard used by SCE as part of the Mohave-Lugo system. SCE will retain ownership of the equipment in the already-fenced capacitor yard.
Coal Supply System. Coal is supplied to the MGS in the form of a slurry consisting of 50% coal and 50% water. The coal slurry is delivered by the Black Mesa Pipeline Company, which has a capacity of 660 tons per hour of coal at a solids density of 48%. The 273-mile long, 18-inch diameter pipeline originates on the Black Mesa in the northeast part of Arizona. The pipeline starts at an elevation of 6,000 feet and ends at an elevation of 750 feet. The coal slurry is delivered from the Peabody Coal Companys open pit mine to the MGS. The pressure and flow rate of the pipeline are maintained by four pump stations.
Coal Slurry Pipeline System. The pipeline system is divided into four sections corresponding to each pump station.
Section 1 begins at the Kayenta Pump Station and continues to the Gray Mountain Pump Station.
Section 2 begins at the Gray Mountain Pump Station and continues to the Williams Pump Station.
Section 3 begins at the Williams Pump Station and continues to the Seligman Pump Station.
Section 4 begins at the Seligman Pump Station and ends at the MGS.
In order to increase the pressure drop through the system prior to entering the station, the 18-inch diameter pipeline reduces in size to 12-inch diameter at the top of the mountains just east of the MGS.
Black Mesa Pipeline Company performed a study of the pipeline system in 1996 utilizing internal sonic measurements to identify sections requiring repair or replacement. This study identified 31 locations where thinning of the pipe had occurred. The sections identified in this study have been replaced. In addition, 3 miles of pipe was replaced in 1998. Sections 3 and 4 of the pipeline transportation system have experienced a total of 10 line failures during the past three years. An additional 18 miles of pipe requiring repair or replacement has been identified. These upgrades would be made by Black Mesa Pipeline Company.
The coal slurry pipeline enters the MGS fenceline on the east side of the cooling tower area and continues in a westerly direction to the south of Unit 1. The entire pipeline is owned by the Black Mesa Pipeline Company.
Installation of a Bag House and Scrubber
The Sierra Club and Grand Canyon Trust filed a lawsuit regarding the air emissions from the MGS. The National Parks Conservation Association later joined as an additional plaintiff. In settlement of that lawsuit SCE and the remaining co-owners of the MGS have agreed to provisions of the consent decree that has been entered and served by the U.S. District Court, District of Nevada.
The settlement includes provisions that the MGS, if it remains in operation as a coal-fired plant past 2006, will be retrofitted with a dry scrubber (with lime spray technology or equivalent control equipment), and a polishing bag house (fabric filter dust collector). These pollution controls are required to substantially reduce sulfur dioxide (SO2) emissions and opacity. The consent decree specifies that opacity limits will be reduced to 20% from the current 30%. The SO2 limitation will limit emissions to 0.15 lbs. of SO2 per British Thermal Unit (BTU), on average. An 85% reduction efficiency would also be required for SO2 (reduction efficiency reflects the percentage reduction in SO2 levels from those in the flue gas entering into the control equipment compared to air emissions from the control equipment).
The consent decree specifies that if any of the four current co-owners of the MGS continues to own any portion of the plant, the new emission limits will be met by January 1, 2006, for one unit, and April 1, 2006, for the other unit. If no current co-owner retains ownership and the sale transaction is completed by December 30, 2002, then the new emission limits must be met within three years of the last sale for one unit and three years and three months for the second unit. Note that this arrangement is independent of the sale of the MGS proposed by SCE pursuant to AB 1890, but the sale of SCEs interest could contribute to an earlier emission control installation date.
The tendency of new owners who do not have other generating assets in a region to increase operations has resulted in installation of new emission control equipment at many of the coal-fired power plants sold across the USA and overseas. At the MGS, this trend could lead to the installation of a bag house and scrubber somewhat earlier than the timeframes described in the consent decree (however, SCE has suggested this schedule will be physically difficult). |
|